In the pharmaceutical industry, the efficient and consistent production of high-quality drug formulations is of paramount importance.
One crucial aspect of pharmaceutical manufacturing is the granulation process, where fine powders are transformed into granules to improve flow, compression, and uniformity.
The High Shear Mixer Granulator (HSMG) has emerged as a key equipment in this process, offering precise control over granule characteristics. This article delves into the working principles, advantages, challenges, and applications of the High Shear Mixer Granulator.
Working Principles:
The High Shear Mixer Granulator combines two vital processes – mixing and granulation – into a single unit operation. The system consists of a cylindrical vessel equipped with a high-speed impeller and a chopper.
The impeller generates vigorous vertical and horizontal movement, causing powders, binders, and other additives to be thoroughly mixed. Simultaneously, the chopper, with its high-speed rotational blades, breaks down agglomerates, ensuring uniform granule size distribution.
As the impeller agitates the powders, the liquid binder is added, forming wet mass granules. The combination of high shear forces and proper binder distribution results in the formation of granules with controlled density and porosity.
The subsequent drying process removes excess moisture, yielding granules with optimal characteristics for downstream processes like tableting or capsule filling.
Advantages of High Shear Mixer Granulator:
- Uniform Granule Formation: The high shear forces and intensive mixing in HSMG lead to homogenous granules, reducing the risk of content non-uniformity in the final drug product.
- Enhanced Dissolution: Uniform granule size and distribution contribute to improved drug dissolution, a critical factor influencing bioavailability.
- Time and Cost Efficiency: Combining mixing and granulation in a single machine streamlines the manufacturing process, saving time and operational costs.
- Process Control: HSMG allows precise control over impeller speed, chopper speed, binder addition rate, and drying conditions, enabling the production of granules with specific properties.
- Scale-up Potential: The process parameters established on a small scale can be effectively scaled up, ensuring consistency from development to commercial production.
Challenges and Mitigations:
- Blend Uniformity: While HSMG promotes uniformity, poor powder blend uniformity can still affect the final product. Proper pre-blending and selection of suitable excipients can mitigate this issue.
- Granule Size Distribution: Achieving the desired granule size distribution requires careful adjustment of process parameters, such as impeller speed and binder addition rate.
- Equipment Design: Ensuring that the vessel design and impeller-chopper configuration align with the desired production scale is essential for maintaining process efficiency.
- Dust Emission: The high-speed movements within the granulator can lead to dust emission. Adequate containment systems and exhaust ventilation are crucial to maintain a safe working environment.
Certainly, here's a table summarizing the critical parameters that require monitoring and control in a High Shear Mixer Granulator (HSMG):
Parameter | Description and Importance | Monitoring Method | Control Method |
Impeller Speed | Influences mixing and shear forces. | Tachometer or Encoder | Variable Frequency Drive (VFD) |
Chopper Speed | Affects granule size distribution. | Tachometer or Encoder | Variable Frequency Drive (VFD) |
Binder Addition Rate | Crucial for uniform binder distribution. | Gravimetric or Volumetric Feeders | Control System or Operator Input |
Temperature | Impacts drying process and granule properties. | Temperature Sensors | Control System or Operator Input |
Humidity | Aids in understanding drying conditions. | Humidity Sensors | Control System or Operator Input |
Powder Bed Height | Ensures uniform mixing and granulation. | Ultrasonic or Laser Sensors | Control System or Operator Input |
Torque and Power | Provides insights into granulation process. | Load Cells or Torque Sensors | Control System or Operator Input |
Pressure | Monitors pressure changes during drying. | Pressure Sensors | Control System or Operator Input |
Vacuum | Monitors vacuum during drying phase. | Vacuum Sensors | Control System or Operator Input |
Granule Size Distribution | Real-time data on granule sizes. | Inline Particle Size Analyzers | Control System or Operator Input |
Applications:
High Shear Mixer Granulators find applications beyond pharmaceuticals, including the food, chemical, and cosmetic industries. In food production, HSMGs are used to create granules for instant beverages or seasoning blends. In the chemical sector, they are employed to produce granulated fertilizers or detergent formulations. Cosmetic companies utilize HSMGs to manufacture granulated skincare products.
Challenges and Considerations:
- Sensor Compatibility: Selecting sensors compatible with the process environment (moisture, powder, etc.) is essential for accurate readings and durability.
- Calibration and Maintenance: Regular calibration and maintenance of sensors and instruments are crucial to ensure data accuracy and reliability.
- Data Management: Handling the volume of data generated by multiple sensors requires an effective data management and analysis strategy.
- Integration: Integrating different sensors, controllers, and data acquisition systems into a coherent control system can be complex and requires careful engineering.
The pharmaceutical sector's growth was a significant driver of the HSMG market. The need for efficient granulation processes to ensure consistent product quality and meet regulatory requirements played a crucial role.
The HSMG market was expected to continue growing due to ongoing advancements in pharmaceutical manufacturing, the drive for more efficient processes, and the integration of automation and data analytics.
As the pharmaceutical industry expanded and technology evolved, HSMGs were anticipated to play a crucial role in ensuring high-quality granules for drug formulations.
Stringent regulatory requirements and the importance of product quality pushed pharmaceutical manufacturers to invest in equipment that could ensure uniform granules and accurate process control.
he ability to customize HSMGs for specific formulations and the successful scale-up of processes from development to production added to the appeal of these machines
Conclusion:
The High Shear Mixer Granulator plays a pivotal role in the pharmaceutical and various other industries, offering efficient granulation while ensuring uniformity and process control. Its integration of mixing and granulation processes streamlines manufacturing, enhances product quality, and contributes to the development of diverse products across sectors. As technology continues to advance, the High Shear Mixer Granulator is poised to remain a cornerstone of modern powder processing.
Rapid Mixer Granulator, High Shear Mixer Granulator, High shear granulation
Rapid Mixer Granulator (RMG) High shear granulation is a multi-purpose processer equally suitable for high-speed dispersion of dry powders, aqueous or solvent granulation, and effervescent products and melt palletization. In a rapid mixer granulator, the formation of granules occurs by rising, whirling, and tumbling motion of the material. Dry mixing is done by adding all ingredients into the RMG by rotation of impeller and chopper at high speed.
High Shear Mixer Granulator is designed to meet the special needs of drying of Pharmaceuticals (Formulations and Bulk Drugs). It offers a controlled, channelized process in a quest to achieve product homogeneity, fluidity, stability by lower heat transfer, clean & hygienic air medium using pneumatics, superior MOC, proven manufacturing expertise and application of cGMP at all stages.

High Shear Mixer Granulator, Rapid Mixer Granulator Manufacturer
Features
- Unique design incorporating Impeller, Granulator, Online Co-mill, Side discharge valve & dryer.
- Internal and External surfaces of Mixing Bowl, Mixing Bowl cover, Impeller, Granulator and Discharge Chute constructed in SS 304/316L.
- Specially mounted torque sensor arrangement for critical parameters of granulation like end point determination & desired granule profile
- Impeller Lifting Options:
- Pneumatically Operated Bottom Impeller Lifting for ease of cleaning.
- Electromechanical impeller lifting and removing mechanism.
- Hydraulically operated Lid lifting.
- Parts easy to dismantle, clean and re-assemble.
- Pneumatics pre-tubed
- Gaskets of Teflon / Silicon
- Bowl surface finish of 0.3RA (inside / outside)
- ATEX Compliant option available
- Customized capacities available
- Optional features of Jacketed models, Vacuum / Gravity Charging, Mechanical Seals, Binder spraying systems, CIP / WIP systems, Vacuum drying, Scada Solutions available
- Drying under vacuum, at lower temperature with solvent recovery system
- Optional features for dryer include PLC control with printer, Turnkey with hearing, vacuum and solvent recovery system
- Multiple options available for Impeller blade, Chopper and Co mill blade and screen
- In-house pressure tested 2 Bar HSMG
- Capacity – 10 – 1200 Ltrs
- cGMP Model and Design as per ASME guidelines
- MOC-SS304/ SS316/ SS316L
- Hydraulically operated Lid lifting
- Detachable Impeller and Chopper
- Qualification Documents – IQ, DQ, OQ and FAT Protocol
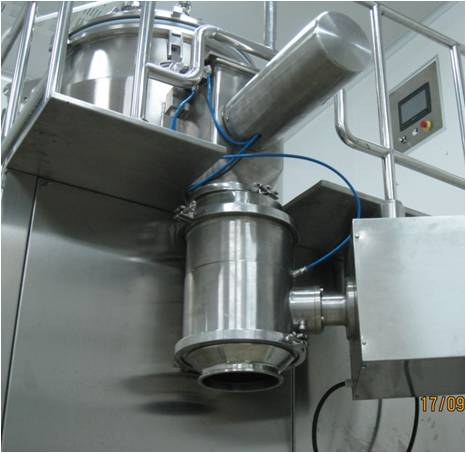
Rapid Mixer Granulator, High Shear Mixer Granulator | Shree Bhagwati
- Optional Items/ Accessories
- PLC with HMI/ SCADA
- 21 CFR Part 11 – Provision and Compliance
- Co-Mill attachment
- VFD
- FLP Motor and Panel